Ensuring that joining technology is sustainable
If we look globally at developments in the automotive industry, we can see that the weight of new passenger cars and light commercial vehicles in Europe has risen constantly in recent years from approx. 1,268 kg in the year 2000 to 1,360 kg in 2010 and to approx. 1,420 kg in 2020. The trend toward more hybrid and electric vehicles is likely to intensify this development because an electric vehicle weighs on average 300 kg more than a vehicle with a conventional engine due to the weight of the battery alone.
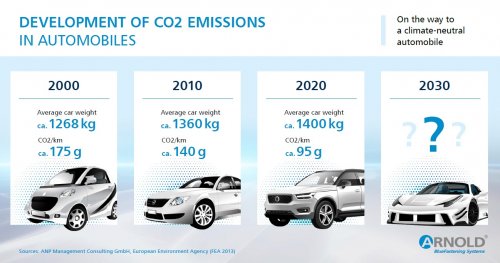
However, due to the optimization of fuel consumption and innovative new powertrain designs, a significant reduction in CO2 emissions has been achieved, from about 175 g CO2/km in the year 2000 to 140 g CO2/km in 2010 and 95 g CO2/km in 2020. This trend must continue if the goals for climate protection for the next few years are to be achieved.
In this context, the issue of sustainability is a major priority for the ARNOLD GROUP from Germany. Alongside e-mobility, internationalization, lightweight engineering and digitalization, it is one of their five defined strategic thrusts.
The company's experts know that an individual carbon footprint is created for each product by looking at the whole value chain and cumulating the emissions of all supply chain members. This means that companies that are downstream in the supply chain add the emissions of their suppliers via the products and services they purchase and then pass these on to their customers, added to their own CO2 emissions.
ACO2-Save offers many different ways of reducing CO2
Against this background, Arnold Umformtechnik has launched the ACO2-Save initiative. (The A here stands for Arnold.) The program provides active support to customers in reducing CO2 emissions by designing and applying fasteners and cold-formed parts in a sustainable manner. Already during the product development process, an accompanying CO2 calculation is performed. When customers request Arnold to make a part, the product carbon footprint can be determined using a specially developed CO2 calculator, after which optimization can be carried out jointly. The objective is to have a technically high-quality product at the end of the development process that is both cost and CO2-optimized.
The design process includes the following steps: CO2-optimized engineering through digital forecasting tools, analysis of CO2 optimization by potentially making a change in the production technology or a change in joining technology, and the use of innovative joining elements or systems.
And it is exactly this ACO2 Save approach that works, as shown by this example: A special screw made of aluminium with a volume of 8,733 mm3 and a weight of 23.58 g per piece was previously produced by traditional machining. A turned part blank was used for production, with an initial volume of 25,630 mm³ and a weight of 69.2 g for each part. After an ACO² Save analysis, this part was changed over to a formed part from the Conform Next product line. The result: After optimization, the forming blank has just a volume of 9,135 mm³ and 24.82 g per piece. In addition to the significant cost optimization resulting from the lower material input during cold forming, this has a considerable impact on the product carbon footprint of the special screw.
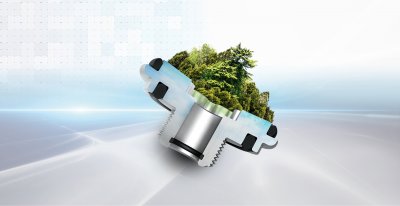
Thanks to ACO2-Save and by making the associated changes to the production technology, gains in Germany’s energy efficiency were achieved and the CO² emissions generated in the production of this screw during production were reduced by as much as 45 percent.
Editor/ Author:
Annedore Bose-Munde is a specialist editor for business and technology in 99094 Erfurt, Tel. (03 61) 78 94 46 95, info@bose-munde.de, www.bose-munde.de
Annedore Bose-Munde is a specialist editor for business and technology in 99094 Erfurt, Tel. (03 61) 78 94 46 95, info@bose-munde.de, www.bose-munde.de
The Arnold Group is a fully owned subsidiary of the internationally active Würth Group, which realises sales of more than 8 billion euros worldwide with 420 companies and about 65,000 employees.
www.arnold-fastening.com